At CMCRL, we focus on understanding the environmental degradation of a wide range of materials from additively manufactured alloys to materials used in molten salt nuclear reactor applications
1. Stress Corrosion Cracking of High Strength Aluminum Alloys
Aluminum alloys are increasingly replacing the steel in automotive vehicles due to its high strength to weight ratio. Unfortunately some of these high strength aluminum alloys suffer from various structural forms of corrosion such as intergranular and stress corrosion cracking at peak aged tempers.
Our group works on understanding the effect of composition and processing conditions on the microstructure of high strength aluminum alloys resulting in stress corrosion cracking and corrosion fatigue.
2. Corrosion and Mechanical Behavior of Additively Manufactured Aluminum Alloys
Additively manufactured high strength aluminum alloys are promising candidates for the aerospace, defense, and the automotive industries. However, the corrosion and mechanical behavior of high strength aluminum alloys are not well understood with various post processing treatments.
Our research group focuses on multi-scale microstructural characterization along with local and bulk electrochemical tests to understand microstructural origins of corrosion and its mechanism in additively manufactured aluminum alloys.

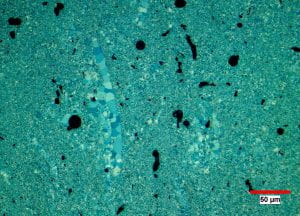
3. Corrosion of Structural Materials in Molten Fluoride Salts
Molten Fluoride salts are considered as candidate coolants for application in next generation Molten Salt Nuclear Reactors and Concentrated Solar Power Plants due to their ability to operate at high temperatures with low vapor pressure, leading to better safety and efficiency. However, corrosion of structural materials in these salts is a major concern for these applications.
Our research group focuses on performing chemical and electrochemical tests and advanced characterization techniques to measure, test, and understand the effect of redox potential on the corrosion of structural alloys in molten fluoride salts and how it is affected by changes to the salt conditions as well as presence of impurities.
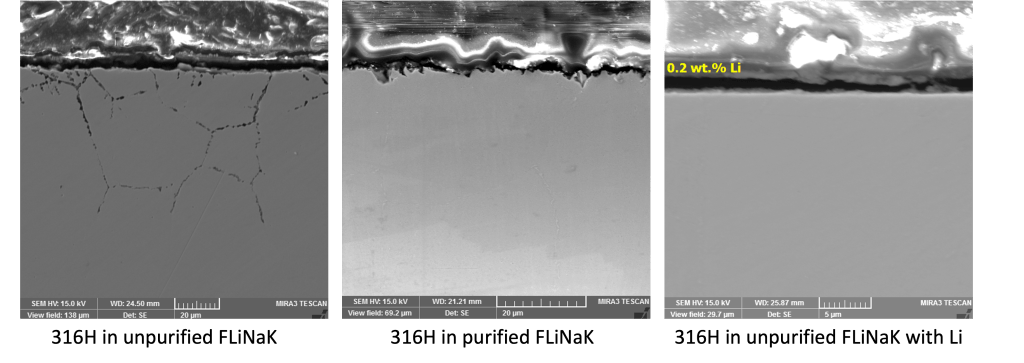
4. Corrosion of Ni and Fe based Alloys in Molten Chloride Salts
Over the past ten years, there has been growing interest in developing and building “next-generation” concentrating solar power (CSP) systems that operate above 700°C. Current heat transfer and thermal energy storage media (typically thermal oils and nitrate salts) are incapable of this increased operating temperature; chloride salts have been tapped as an alternative due to this favorable storage properties and higher thermal stability compared to current nitrate salts. However, the interface between molten chloride salt and structural materials used for the piping, thermal energy storage tanks, and heat exchanger is still a matter of study in the CSP community.
Our research group utilizes long-term immersion testing and SEM/EDS, XRF, XRD, and mass change analysis to characterize the corrosion behavior of the alloys. Experimental data from the ten tested alloys will contribute greatly to the current chloride salt corrosion literature.
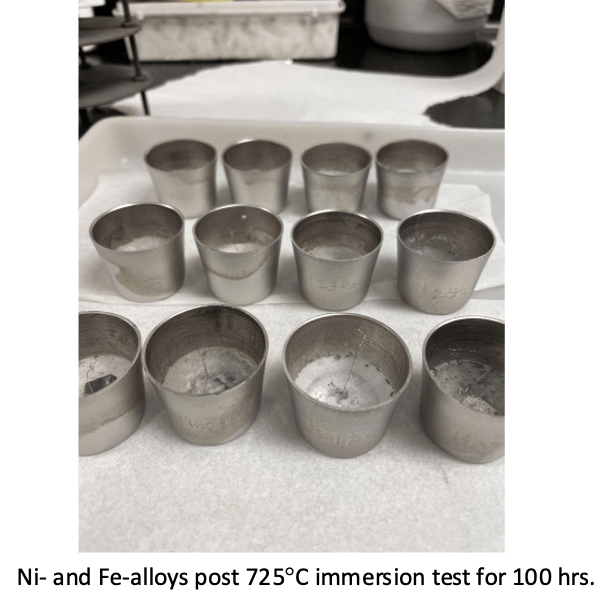
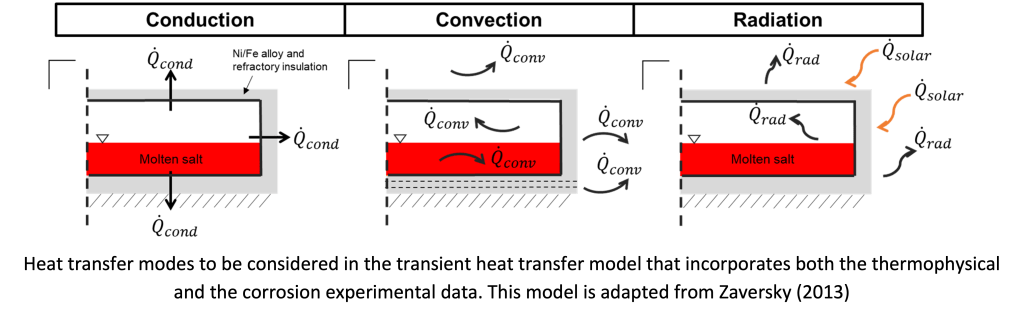
5. High Temperature Corrosion of Alloy Steels
Chromium and vanadium enhance the material performance in high temperature applications. Therefore, a higher chromium content with the presence of vanadium was systematically tested to see if this alloy can replace the current design of hydroprocessing reactors and eliminate the need of stainless-steel overlay. This will help with lower manufacturing and maintenance cost.
This research project focuses on simulating the reactor environment and evaluate these material’s performance. In addition to that, advanced characterization techniques such as XRD, SEM, and EDS were utilized to measure, test, and understand the effect of high temperature corrosion on the selected alloys.
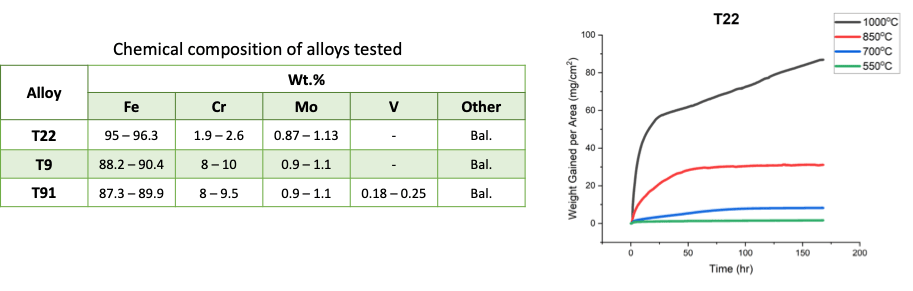
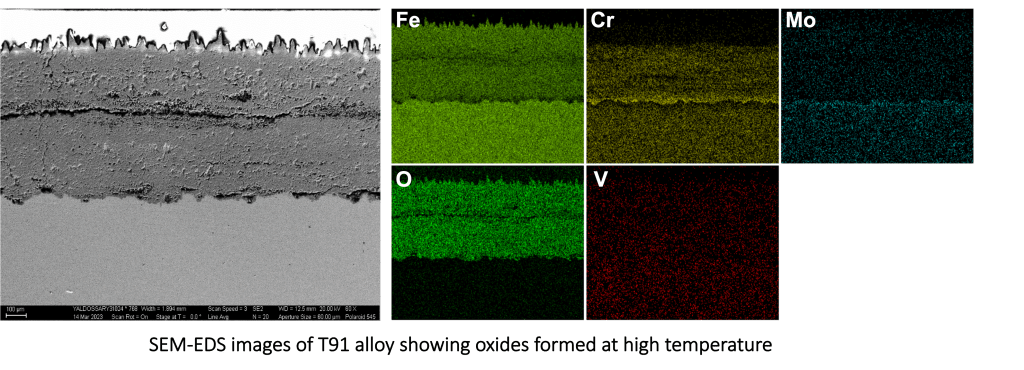